What methodologies do you use for process improvement?
I typically use Lean, Six Sigma, and Agile methodologies to streamline processes and eliminate inefficiencies.
Can you describe a successful process improvement project you've led?
In my previous role, I led a project that reduced processing time by 30% by identifying bottlenecks and implementing Lean strategies.
How do you identify areas that need process improvement?
I use data analysis, stakeholder interviews, and observation to pinpoint inefficiencies and areas for improvement within a process.
What tools do you use for process mapping?
I often use tools like Microsoft Visio, Lucidchart, and Miro for process mapping and visualization.
How do you handle resistance to change when implementing new processes?
I address resistance by involving stakeholders early in the process, ensuring clear communication, and demonstrating the benefits of the change.
How do you measure the success of a process improvement initiative?
I measure success through key performance indicators (KPIs) that align with the project goals, such as cost savings, time reduction, and quality improvement.
Describe your experience with Six Sigma.
I am Six Sigma Green Belt certified and have used the DMAIC framework to enhance process efficiency in various projects.
How do you prioritize which processes to improve?
I prioritize based on impact, feasibility, and alignment with business objectives, often conducting a cost-benefit analysis to aid in decision-making.
What role does data play in process improvement?
Data is crucial as it provides evidence for decision-making, helps identify patterns and trends, and measures the outcomes of process changes.
How do you stay updated with the latest trends in process improvement?
I stay updated by attending industry webinars, pursuing relevant certifications, and participating in professional networks and forums.
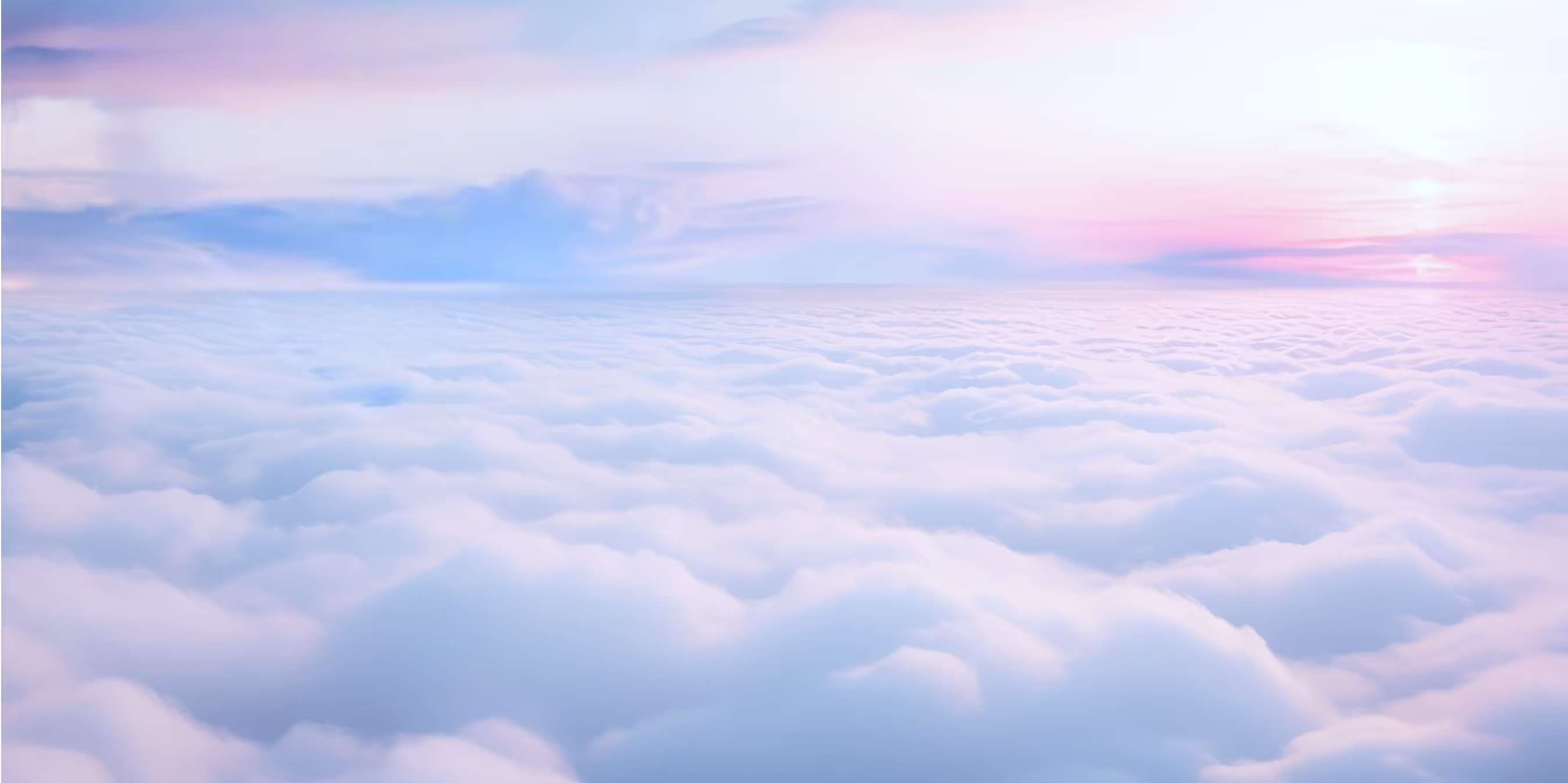
Take practice AI interview
Put your skills to the test and receive instant feedback on your performance